We are in the process of building a luxury custom home on Chilliwack Mountain. We have just passed the halfway point on this home with the completion of the rough-ins. So here’s a quick update of what’s been accomplished so far:
Excavation and Installation of ICF
We started this project with the excavation and installation of the ICF foundation. There is bedrock located on this site and the slope is very steep. Our geotechnical engineers required us to connect the foundation to the bedrock with rebar anchors that we epoxied into the rock.
After the foundation was completed, we moved onto the remaining site work. This included: perimeter drainage and damp-proofing of the foundation; installation of a storm water management system; a septic system; and prepping the site for a one piece fibreglass pool. Finally, we installed a large Ankora retaining wall system to support the driveway.
Structural Framing
Our next step was structural framing. On this project, we partnered with Paradigm Building Solutions and used their factory-fabricated wall panels. This drastically sped up the framing process. It enabled us to install the exterior wall panels for each floor in less than a day per floor!
The floors were then framed with open web floor trusses. They provide a lot of space for ducting, plumbing and electrical and they eliminate any drops in the ceilings.
Roofing
Our roofing contractor installed a two-ply SBS membrane roof over the roof sheathing. Now we were watertight and could start drying out the building. Westeck Windows supplied all the windows and exterior doors for this custom home on Chilliwack Mountain.
All of this meant that the lock-up phase was now complete.
Rough-Ins
Recently, we finished the mechanical HVAC rough-ins, plumbing rough-ins and we are now working on electrical and low voltage.
The rough-in stage is very critical: Every outlet, fixture, duct, etc. must be very accurately placed so that once drywall is installed, they are in the correct location. We spend hours doing the layout and verifying locations of every critical item before we move to the next phase.
Siding
Working on the exterior, our siding crews have started on the Hardi panel fascias. They look fantastic! Meanwhile, the stucco contractor has started on the liquid applied weather and air-barrier. This needs to be done before the installation of the Exterior Insulated Finish Cladding system. (Also known as EIFS.) EIFS uses EPS foam (two inches in this case) behind a layer of reinforced acrylic stucco. This provides excellent energy performance as we essentially create a two-inch insulated blanket around the entire home.
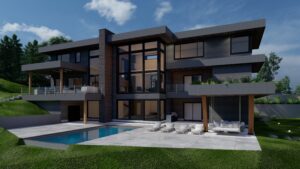
Next Steps for this Custom Home on Chilliwack Mountain
Now, we’re moving onto insulation and drywall on the inside. We’ll also be completing the exterior cladding. This custom home on Chilliwack Mountain is going to be spectacular! For more updates on this project, be sure to follow us on Instagram at @alair604 and @alairhomes.chillwack.